There might come each day when we are purchasing a tube of ink gel for the printers.Xerox on Thursday stated it’s previewing what it really calls a “cured gel ink technology” that prints on plastic and foil.
By Ray Dignan for Between your Lines May 29, 2008 — 05:44 GMT (22:44 PDT) Subject: Printers
There might come each day when we are purchasing a tube of ink gel for the printers.
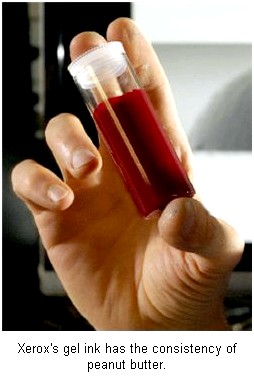
For the time being, this ink gel is fixed to commercial printing–brochures, catalogs, card board packaging and plastic films–but when the study is switched right into a product it might enter into the customer market.
Xerox is showcasing the brand new ink at drupa, a print industry confab. Xerox stated inside a statement:
The brand new cured gel ink holds its shape on nearly any surface since it is not water-based like traditional inkjet technologies. The gel ink has got the consistency of peanut butter after it’s jetted with the print heads and turns rock solid when uncovered to some pulse of ultraviolet light. It makes sense a crisp, vivid, and lengthy lasting image. Unlike current water or solvent-based inkjet systems, the gel ink will not bleed-through or require dryers and vapor recovery systems, therefore increase print speeds and making the machine more eco-friendly. Produced by scientists in the Xerox Research Center Canada, the cured gel inks derive from Xerox’s proprietary solid ink technology.
Xerox emphasized the new ink technologies are still within the research phase, but “it’s clearly an innovation which will take inkjet past the products and applications currently available.”
Xerox’s presentation at drupa is going to be Webcast inside a couple of minutes. In that Webcast Steve Hoover, v . p . and center manager from the Xerox Research Center Webster, gave a summary. Here are a few of his relevant prepared remarks:
The important thing challenges of current inkjet technologies may be the fundamental incompatibility of the advantages of first squirting a lot of it through a little nozzle – the nozzle opening is all about 10 microns or 1/tenth the thickness of the real hair – using the second requirment the ink bond to the top of paper or any other substrate WITHOUT soaking through the paper or distributing within the paper which in turn causes poor picture quality. Both of these needs – ink thin enough to jet through an nozzle – but thick enough not to soak through the paper cannot both be met by current inkjet technologies. It is because to squeeze a give up of the inkjet nozzle the liquid should be concerning the consistency water.
Compare that towards the consistency of lithographic or flexographic inks for like tooth paste. So, current inkjet inks are extremely watery and eject fine from nozzles however when they hit the paper they’re still very thin and they also soak through the paper or spread across the paper fibers causing poor picture quality – unless of course you utilize very costly special papers. Again match it up to lithography or flexography – which let you use any paper, film or foil you would like. It is because individuals inks are extremely thick when printed and provide outstanding picture quality on the wide range of surfaces. Xerography which utilizes a toner that’s mostly plastic which melts inside a fusing step has similar performance to lithographic inks and works with an extensive selection of media for the similar reason – it does not soak through or move about a great deal around the paper. Additionally towards the picture quality and media compatability issues brought on by current inkjet inks being over 90% liquid –frequently water–that liquid also should be taken off the paper after printing. This can lead to large complex and energy drying sytems and when solvent inks are utilized, costly vapor recovery systems. The ecological impact famous that energy consumption to get rid of water or any other liquid should be considered and really should be prevented if at all possible.
All this produced the innovation imperative for that Xerox Research labs: could we develop an inkjet technology which had the advantages everybody wants from inkjet of simplicity, productivity, inexpensive and reliability but combine individuals using the broad media latitude of xerography, lithography and flexography? Could we create an ink which has the consistency water when ejected from your inkjet nozzle however the consistency of tooth paste if this hits the paper and sticks permanently to the substrate – papers, metal foils and plastic films? When we can make this we’ve produced a really disruptive innovation Body that can make a genuine impact on our customers business. The solution we feel is absolutely. Within our labs we’ve produced this kind of ink, a compatible lengthy existence and powerful scalable print mind and also the print process essential to place it altogether. Now again, this really is a classic look within our research labs and we’re still in the technology development stage but we’re so excited that people desired to share this breakthrough along with you.
This can be a microscopic picture of our solid ink in writing. Spot the well created dots – no bleed through – no us dot distributing. Spot the vibrant vibrant colors. It has given our solid inks great performance at work. On standard office papers we’ve no showthrough, vibrant colors with no us dot spread and noise.
But, our current solid ink technologies have obvious limitations for production. For applications that demand low run cost on thin, plain or recycled papers for example transactional/marketing documents solid ink is going to be advantaged because of the inexpensive and superior picture quality over h2o based inkjet. However, around the broader paper range that production customers desire – a multitude of coated papers as well as metal foils and plastic films – a brand new breakthrough is needed. Our solid inks can print on coated papers only on specifically designed papers having a unique coating. For all those reasons I’ve discussed none water, solvent based or our solid inks will come across the entire needs of production to print on an array of papers, foils and flicks. A genuine breakthrough is required to go ahead and take industry where it wants to choose inkjet technology.
That breakthrough is our cured gel ink. This ink is really a liquid having a consistency near water in an elevated temperature – near 100 levels centrigrade – however that has got the consistency of tooth paste if this touches paper or nearly every other substrate – including not just coated papers, but additionally metal foils and plastic films. Then when it contacts the paper it doesn’t soak right through to the rear or disseminate unevenly creating poor picture quality. No, rather it sticks exactly where it lands giving precise and consistent us dot formation and vibrant and vibrant colors and noise free images.
Here the thing is these drops of ink striking the substrate and turning out to be a gel once they hit the paper. They hit and stick, developing precise dots reliably and frequently. However that still is not enough. Not just must the drops stick there once they lands however the final image should be robust. It should be in a position to undergo the rough handling and abuse and elevated temperatures that finished documents for example automobile manuals susceptible to over 70 levels centrigrade inside a automobile glove box, or packaging materials shipped lengthy distances or mail transported across a desert at the back of a truck. So, we add the last step. We expose a lot of it around the paper to Ultra violet light which initiates a compound curing procedure that hardens a lot of it right into a thin robust film in a position to undergo significant abuse and never peel, scratch or chafe even at elevated temperatures.
Together these steps of heating a lot of it to become thin enough to jet, getting a lot of it are a gel the consistency of tooth paste on impact using the surface after which curing a lot of it to obtain a robust and permanent image mean we are able to print on nearly any surface. Here the thing is images from your test fixture showing printing not just in writing, but on obvious plastic film and metal foil. Our cured gel ink technology set breaks previous tension between through an ink thin enough to squeeze with an inkjet nozzle as well as an ink thick enough to do something like lithographic and flexographic inks in writing so you obtain the picture quality you’ll need. And also the curing process provides you with that picture quality permanently supplying a really robust image in a position to survive standard handling practices inside your finishing equipment plus shipping and employ. Also it performs this with no complex and intensive drying or solvent recovery steps other inkjet technologies require.
Source: www.zdnet.com